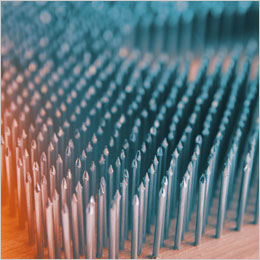
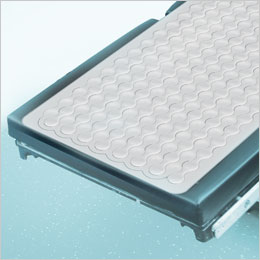
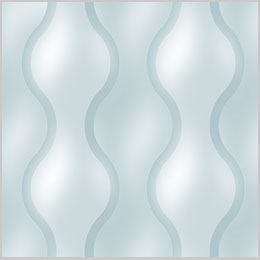
Dabir Surfaces – Medical Device
The Challenge: Innovative Support Technology for Pressure Ulcer (bedsores) Prevention.
Pressure ulcers (PUs) are a tissue injury resulting from pressure or from pressure combined with shear or friction. In the U.S., the annual treatment cost of PUs has been estimated at $11 billion and the cost to manage a single full-thickness PU is $70,000. Dabir technology is based on the principle of supporting a person on small, closely spaced areas of contact (Comfort Nodes) that dynamically alternate in height to relieve support pressure areas. The aim is to preserve the circulatory components of arterial, venous and lymphatic blood flow in between these areas of contact.
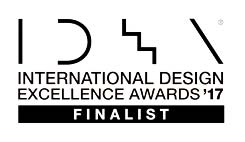
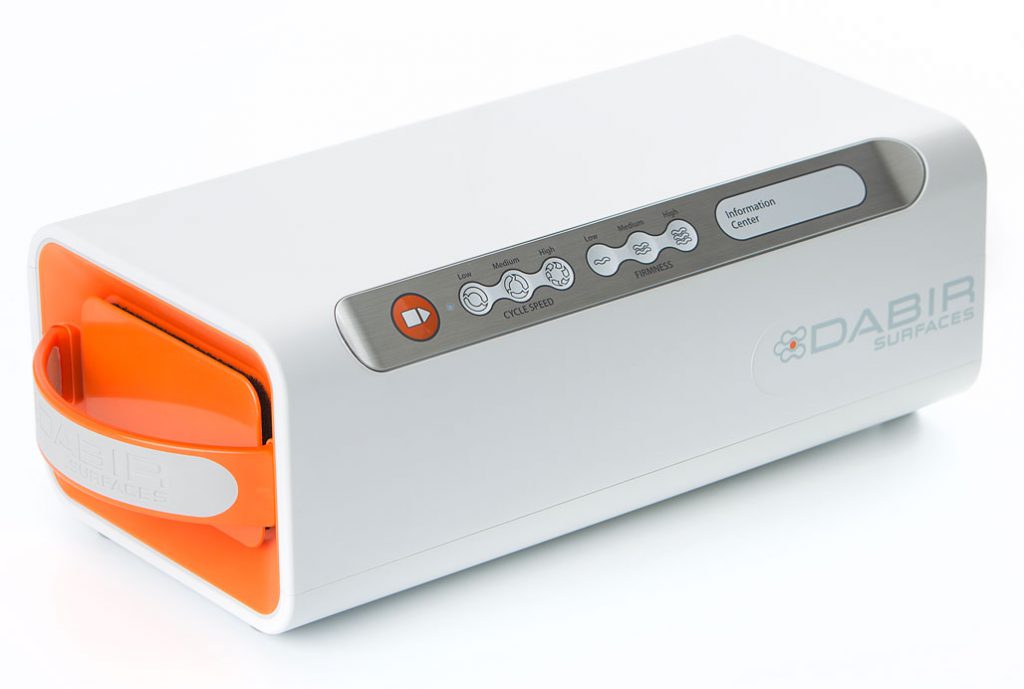

Design Solution: Phase I
The first alternative pressure ulcer prevention solution in over 50 years.
The current standard for a pressure ulcer prevention surface utilizes a proprietary mattress with large, air-filled nodes. These products are inherently large and focus more on comfort rather than providing therapeutic care. Due to their limited capabilities, their controllers were far less sophisticated. The Dabir Surfaces solution uses thin, micro-nodal technology that displaces pressure sensitive areas every few minutes, without causing movement to the patient. In addition, by utilizing micro-nodes, tissue is stimulated to encourage blood-flow (perfusion), and as a result, blood stagnation (bruising) is eliminated. In a hospital environment, a Dabir Controller had to be easy to use, compact, shielded, quiet, rugged and foremost, fail-safe. Beyond the functionality, as part of a premium brand, the aesthetics and form had to adhere to corporate identity standards.
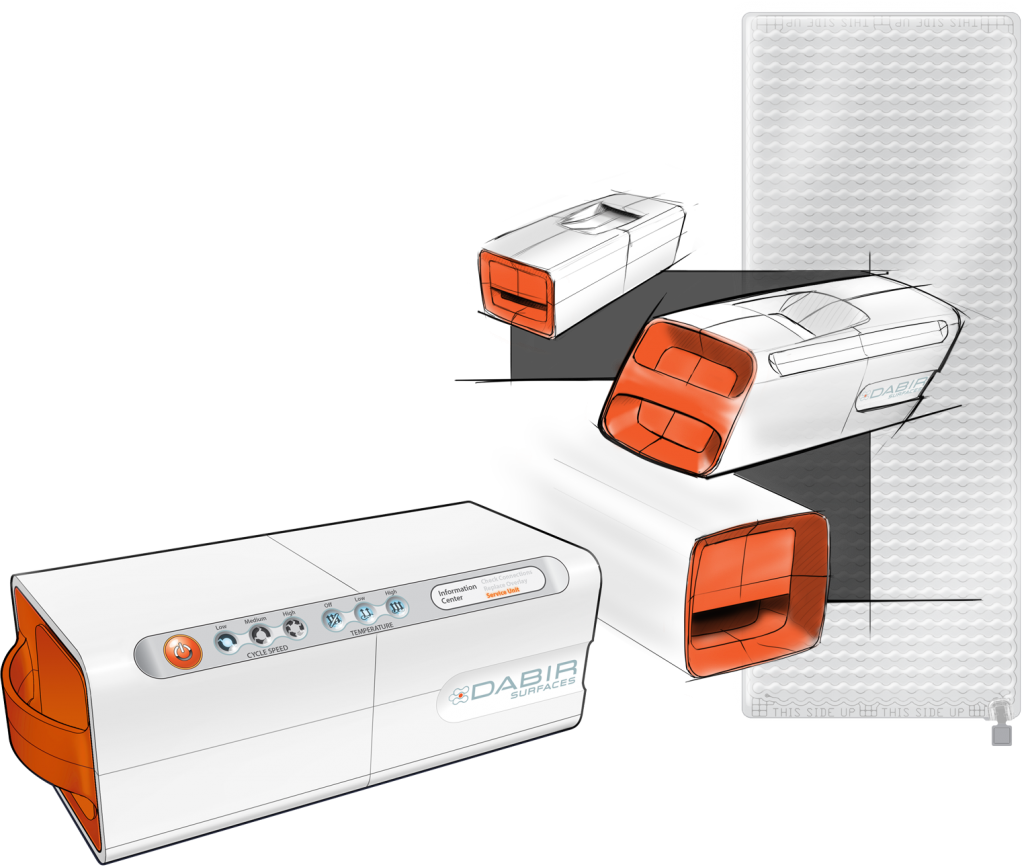
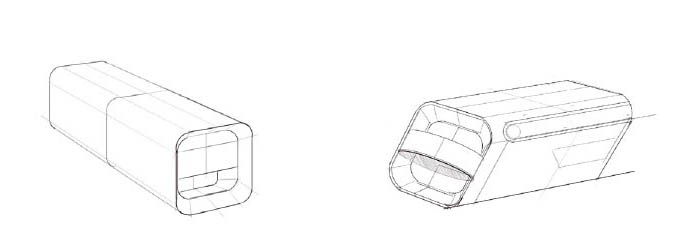
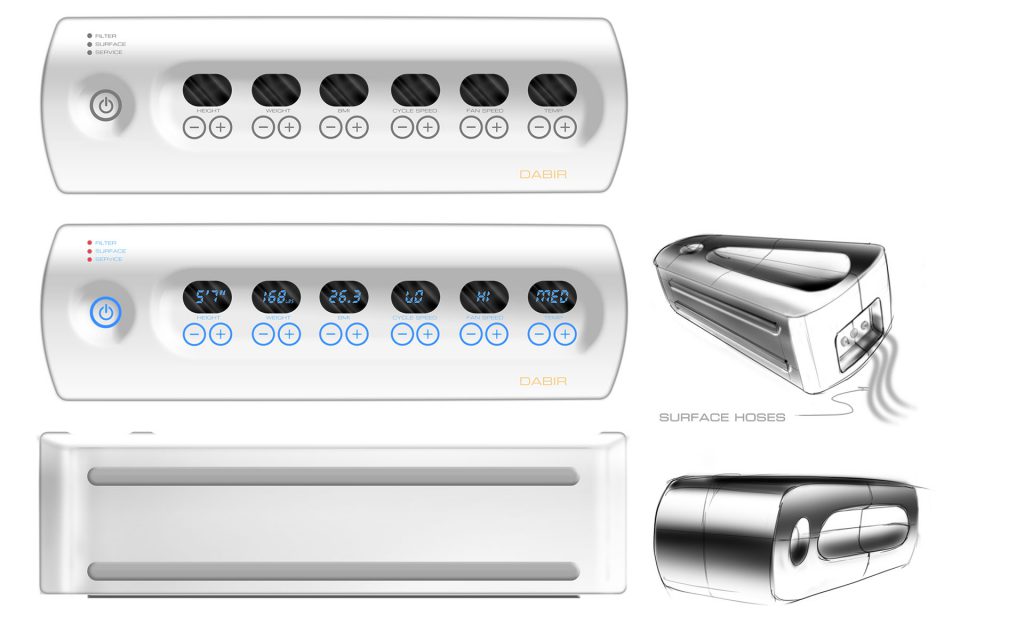

3D Renderings
Design Solution: Phase II
Integrating Design with Manufacturing.
We designed the Dabir Controller to be intuitive, fail-safe and rugged enough to sustain a hospital environment. We created a brand-inspired housing and user interface with a number of innovative A-side and B-side features, such as concealed ventilation, an integrated carrying handle, solid-state touch sensitive electronics and gasket sealed inserts.
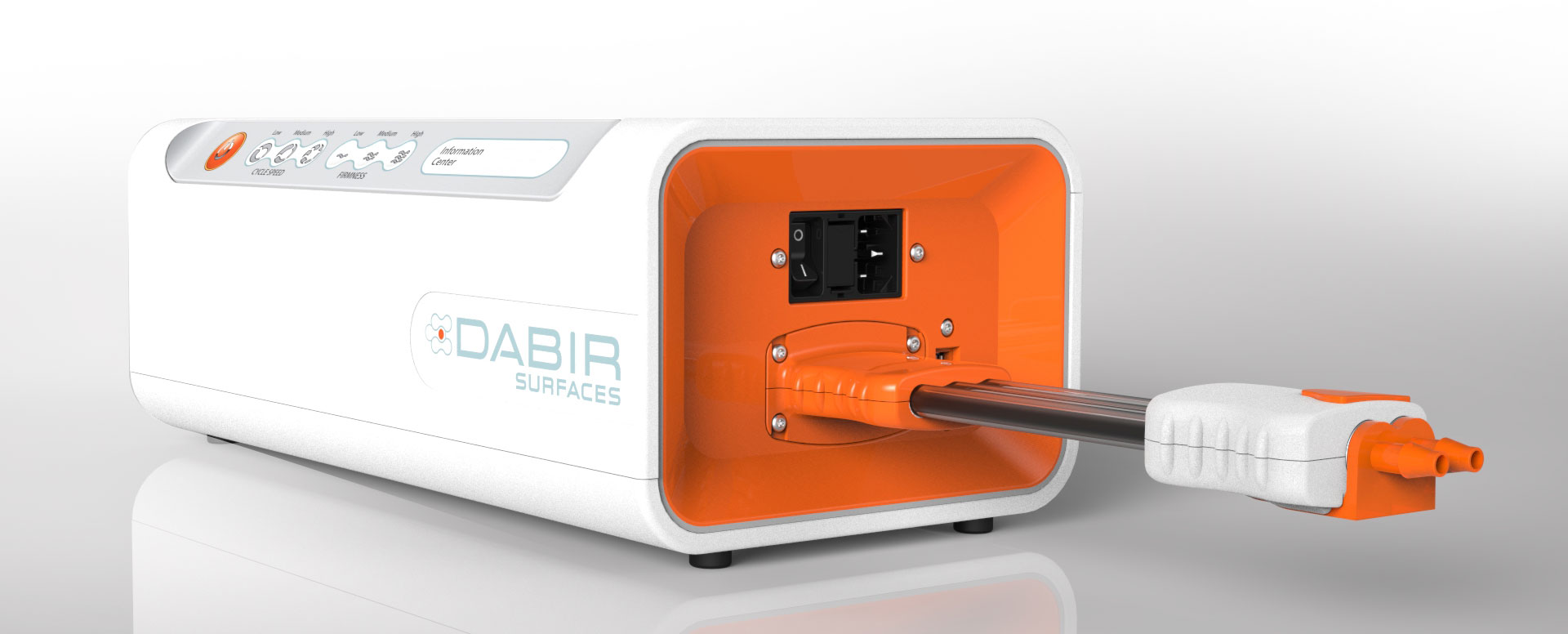
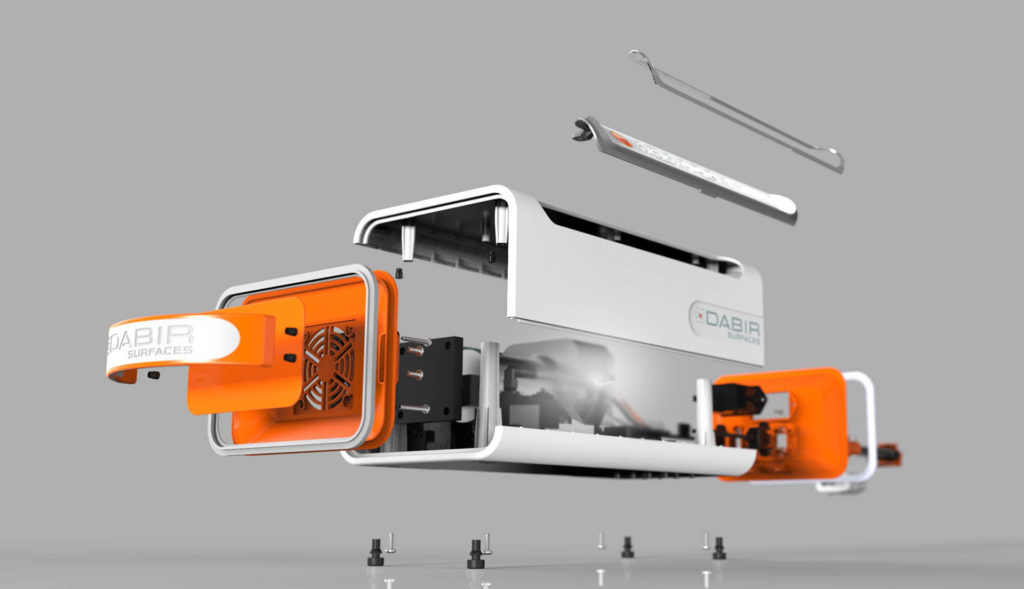
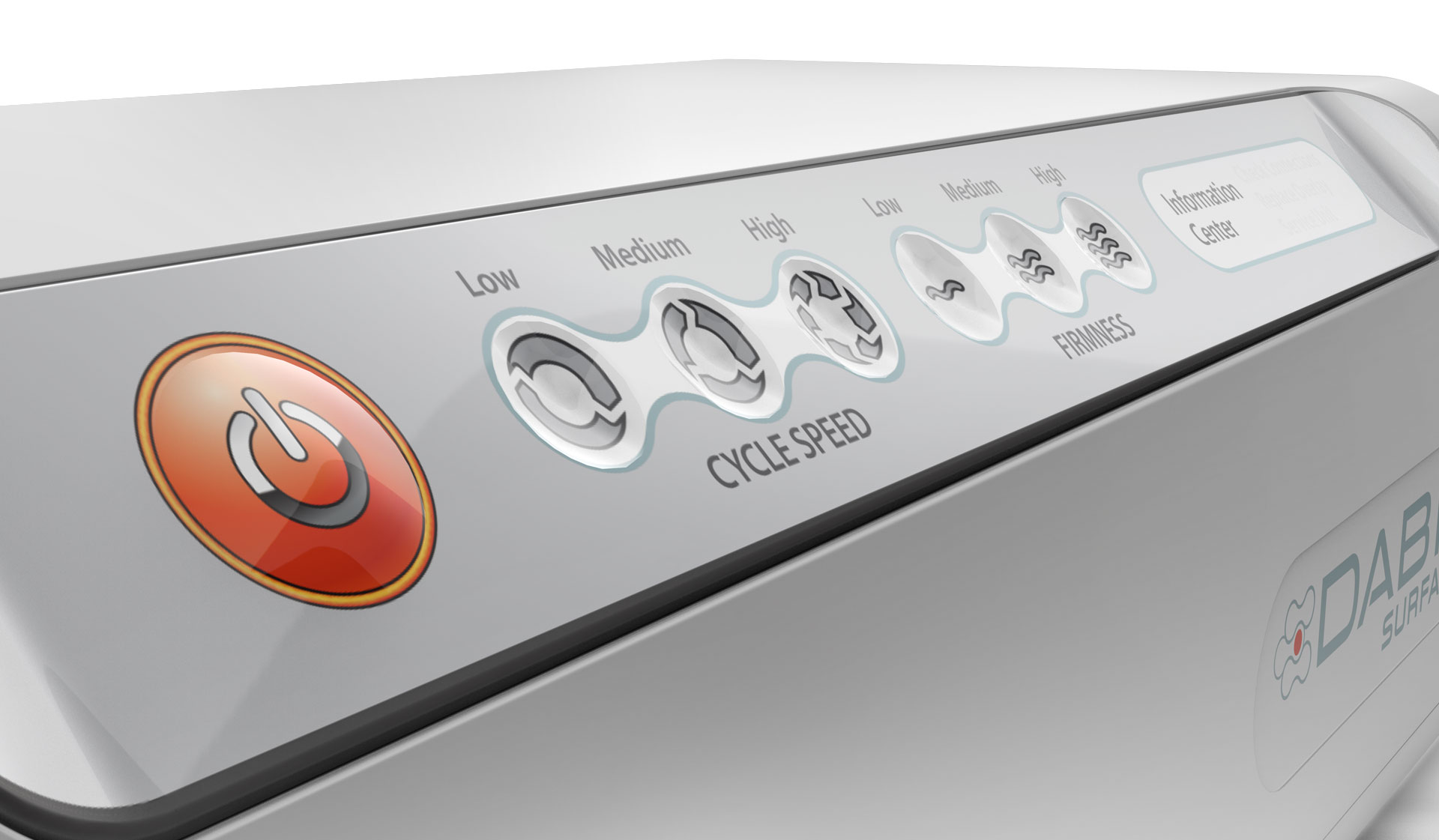

Prototypes
Design Solution: Phase III
Product Testing Starts Here.
In a hospital environment, large, critical equipment can often fight for space near the patient. Even with all the advancements in digital design software, there is still no substitute for a scale model in its environment. We created a number of models to check for scale, as well as accessibility to the user interface. Our modeling capabilities, such as foam sculptures, SLAs and FDMs, cast urethane models and other 3D printed models allow us to test fit and finish and are essential in our usability studies.

Final Product Design
Final Design Solution
Medical Product Design:
In a relatively short amount of time, we produced a system that could immediately be used for testing in the clinical validation process. From tooling to materials, we provided the necessary components to get the product manufactured. The product is now deployed in a number of hospital networks across the country, and studies are proving 100% successful in the elimination of pressure ulcers.
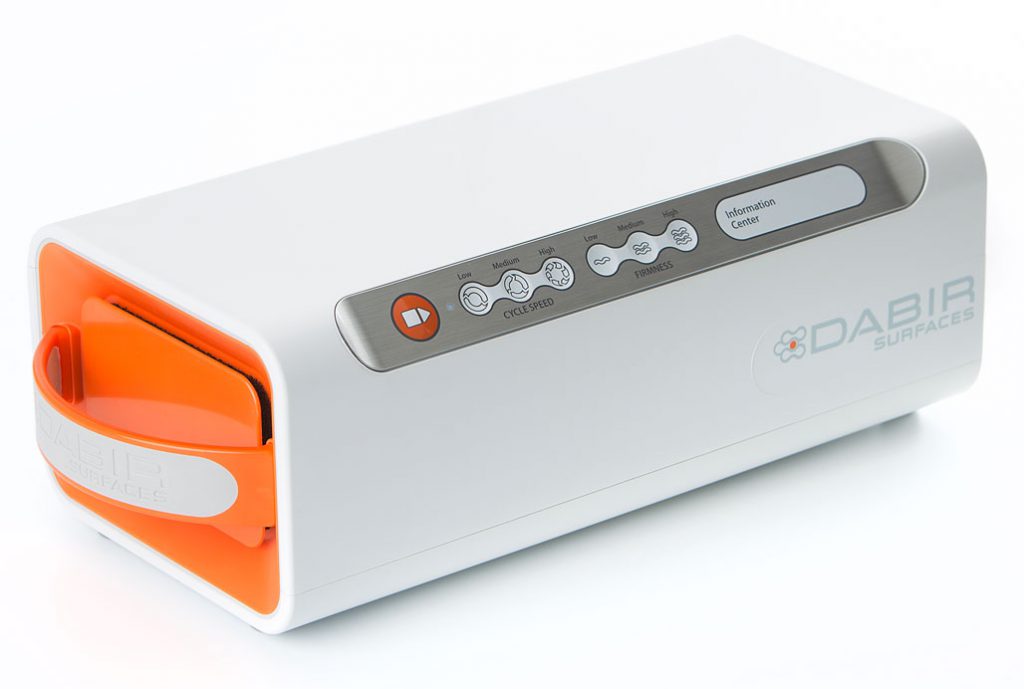
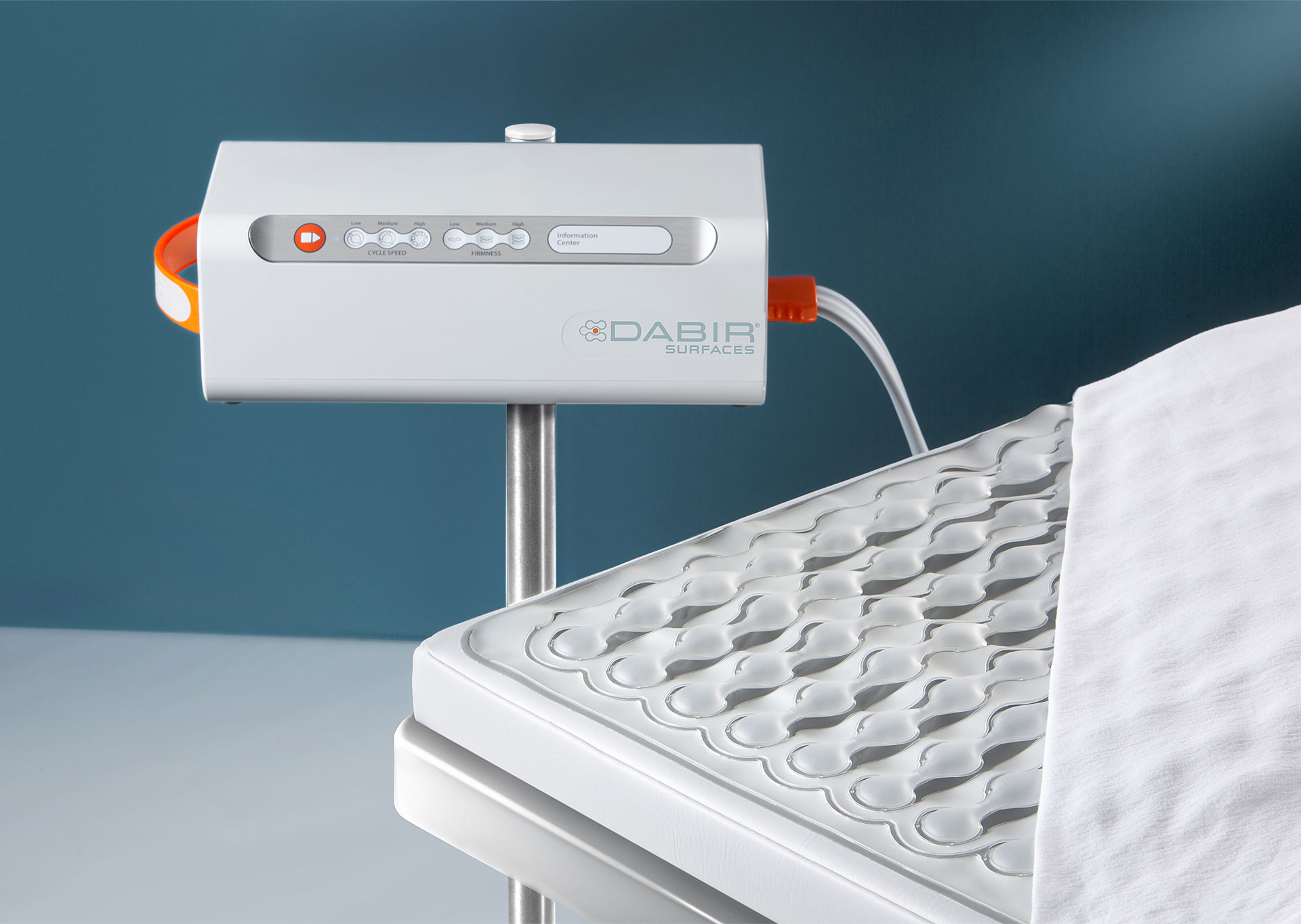